Tata Steel Europe revival hinges on gains from Netherlands’ reorganization
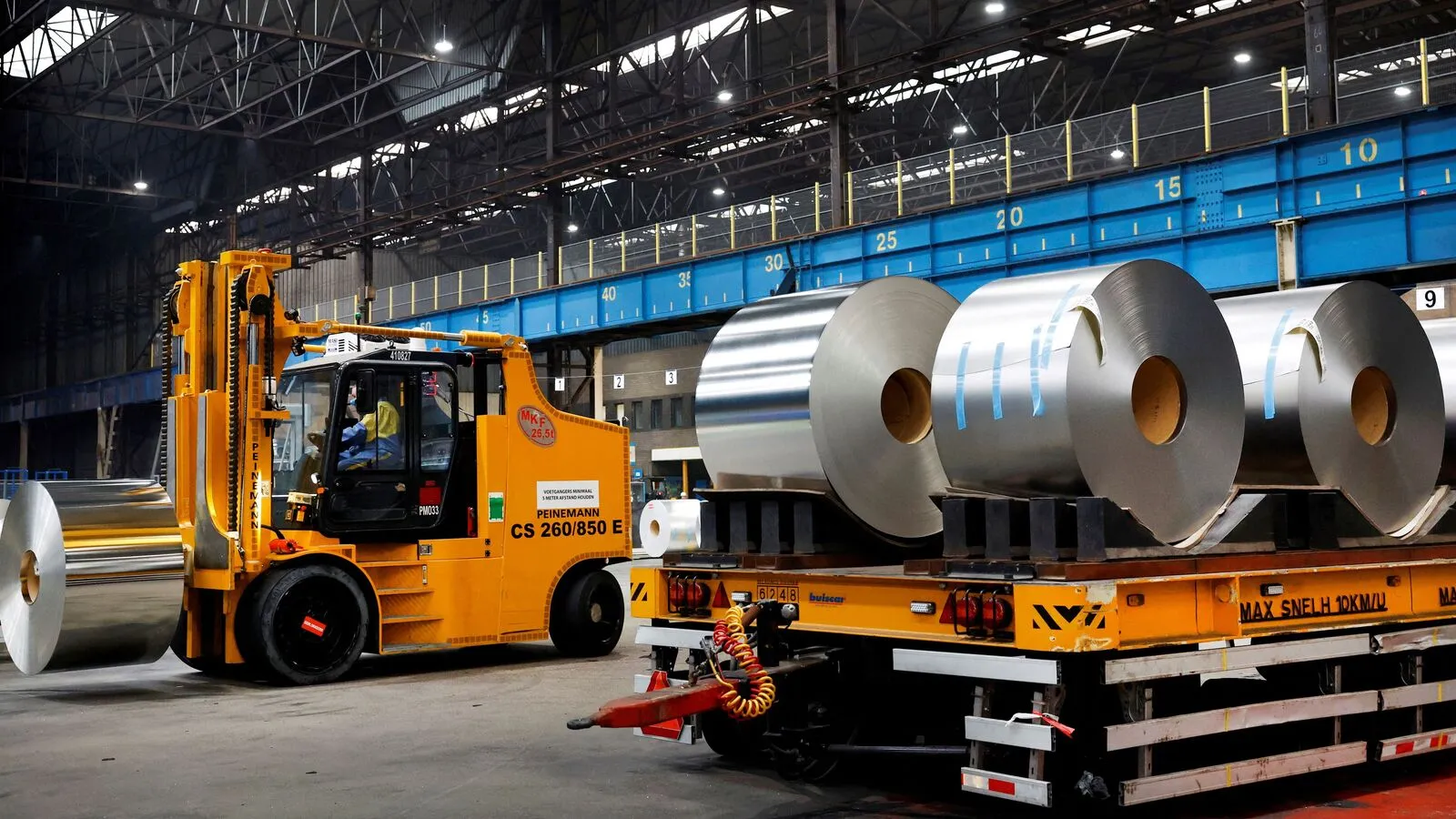
When the going gets tough, the tough get going, and that’s what Tata Steel Ltd is doing. Last week, Tata Steel Nederland announced a crucial transformation programme aimed mainly at reducing costs in the backdrop of tightening spreads in the European steel market.
High energy and carbon costs in recent years have put steel spot spreads under pressure in Europe. As a report by Axis Securities points out, steel spot spreads in Europe were at a multiyear low in Q3FY25 at €170 a tonne versus historical average of €240 a tonne.
Tata Steel’s decision may also have been necessitated by the US’s 25% tariff imposition on steel imports. The company’s Netherlands plant exports about 670,000 tonnes annually out of a total production of 6.8 million tonnes to its downstream subsidiaries in the US, which could be affected by the tariff. The Indian and UK operations have miniscule exposure to the US.
To protect the industry, the European Commission announced certain measures in March, including reducing the duty-free imports quota. Tata Steel’s Netherlands operations have reported negative Ebitda in seven out of the past 10 quarters. Ebitda stands for earnings before interest, taxes, depreciation, and amortization.
The cost reduction plan focuses on improving production and supply chain efficiency, reducing other fixed costs and bringing down the head count by about 18% from the current base of 9,000 for the Ijmuiden plant.
The total cost savings is projected at €500 million in FY26 and an additional €50-60 million in FY27. This includes savings of about €160-180 million from lower employee costs. Employee benefit expenses for the Netherlands plant stood at ₹17,000 per tonne of liquid steel production for 9MFY25 versus ₹3,900 for the domestic standalone business. Similarly, other expenses stood at ₹27,000 per tonne against ₹20,000 for standalone business, providing the headroom for cost control. However, the company said there could be a one-time cost associated with the separation.
A long way to go
Meanwhile, the tripartite discussion with the Dutch government and the European Commission for financial support to transition to green steel is underway, and Tata Steel hopes to issue a joint letter of intent in the next few months. The company plans to build a low-carbon direct reduced iron furnace and an electric arc furnace (EAF) to replace one of the two blast furnaces by the end of this decade. Recall that ArcelorMittal has received similar support for its plants in Europe.
The UK plant, which has been making Ebitda losses for the past 10 quarters, is set to achieve cash break-even in Q2FY26, having achieved about £70 per tonne of cost savings by Q3FY25, out of the targeted £100 per tonne.
Meanwhile, the company has closed both of its high-cost blast furnaces. The downstream units are running with semi-finished products sourced from the Netherlands until the expected commissioning of energy-efficient EAF by 2028.
An Antique Stock Broking report projects Tata Steel Europe (the Netherlands and the UK together) to report an Ebitda per tonne of $33 and $41 in FY26 and FY27, as against a loss in 9MFY25. The company’s domestic operations remain robust, generating standalone Ebitda of close to ₹21,000 crore for 9MFY25, which fell by ₹2,200 crore on consolidation.
Tata Steel’s share price, which had gained 12% in 2025 until the reciprocal tariff was announced by the US, with an improving outlook for Q4, has corrected sharply by 14% since then. Investors would closely watch the cost optimization gains in the Netherlands and the turnaround of the UK operations for further cues. However, rising trade tensions may pose near-term challenges for commodities in general. Thus, investors must closely follow developments on tariffs.